CIRSCO: Pioneering Roof Care Solutions
Maximizing Lifecycles for Fortune 500 Facilities
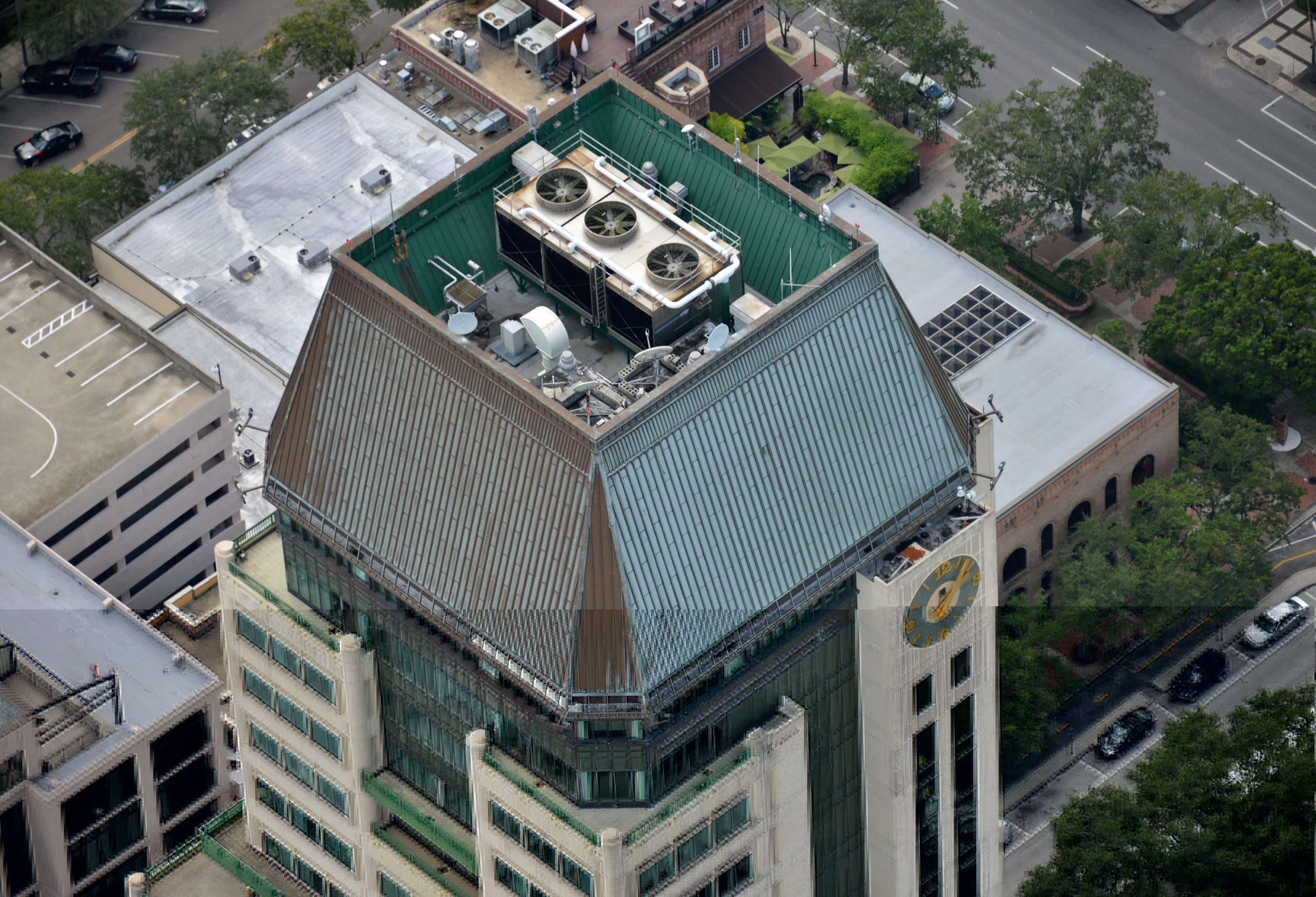
After the information is gathered from the inspection then it’s possible to evaluate the data, measure the roof’s performance, predict future performance and recommend options. This step is critically dependent upon the experience of the person reviewing the information. Roof materials and roof systems perform differently from one building to the next.
It’s important to understand which factors had the greatest effect to bring the roof to its present condition. Building use, environmental exposure, rooftop traffic, nearby facilities, weather exposure, original installation methods, prior attempts to repair and compatibility of the materials are all considerations. There are many hundreds of different roof systems but each facility is truly unique.
Most discussions of maintenance actually include two different sets of recommendations. One set can realistically be called “housekeeping” and those steps can be performed by the facility’s maintenance personnel but are more often performed by roofing contractors. They should be performed whenever the roofing contractor is on the roof.
The second set of recommendations is more related to the specific characteristics of the roof system type. These include the type of materials used, how the system was detailed at the penetrations and perimeter, the components of that particular system that commonly require attention, those materials with typically shorter life spans, the workmanship of the original installation, etc.
There is a great deal of discussion about the value of warranties and the role of maintenance to keep the warranty in force. An internet search for warranties will produce up to 180,000 results and they are on both sides of the “value-of-the-warranty” issue. Keep in mind the warranties were written by the manufacturers to specifically identify their exposure. More importantly, there is no dispute that proper maintenance can increase the life of a roof by 20% – 30% without regard to warrantie
At present, this is probably the most dynamic area of our activity as building owners are concerned that the roof’s life might be over but aren’t prepared for a complete replacement. Restoration involves products that are compatible with the existing system and can re-invigorate the existing materials, bond very well to the existing system and extend the life of the roof for an additional, warranted 5, 7 or 10 years.
Not all roofs can receive a restoration treatment and conditions such as wet insulation and deteriorated flashing areas may need to be addressed but the economics of the appropriate system can make it a viable consideration for older roofs. Additionally, restoration treatments can usually be classified as maintenance and be treated differently than amortizing a new roof system.
To remove an existing roof and replace it with the most suitable system for the building’s exposure is much more difficult than installing new roofs on new facilities. The process requires a great deal of expertise and up-front investigative work so that there aren’t any surprises to the owner once the process begins.
For some contractors it is a much simpler approach to offer a low bid at the beginning and then continuously submit “change orders” after the work has begun. Often, the owner feels “stuck” since the roof is now open and some immediate response is necessary. Ultimately, the original low price could develop into the most costly of the owner’s options.
CIRSCO focuses most of its attention on existing facilities and has the expertise and the methods to thoroughly investigate existing conditions and include those conditions in its proposals. We do not feel that building owners and property managers should have to undergo continuous change orders and do not want to risk our integrity by continuously submitting them.
The entire construction industry is abuzz with “Green” and the U.S. Green Building Council’s LEED rating program is a part of everyday conversations. The roofing industry is very much a part of the movement to sustainability and energy efficiency. But it’s not just a matter of vegetated roofs or white roofs.
Environmentally-friendly also involves how roof materials are made, how scrap materials at the factory and the project site are processed, the potential for re-use of the new materials when that roof’s life-cycle is over as well as the energy efficiency of the system once it’s in place.
The process of replacing an existing roof can also play a role depending on how those materials are re-used or discarded. CIRSCO recently featured a re-roof project in its literature that followed “green” principles and fully accepts its share of responsibility to continue to do so.
It has long been accepted that white roofs reflect heat and darker roofs absorb heat. Today, most manufacturers of roofing products have some form of white materials in their product mix. Metal roofing, single-ply membranes and coatings are available in white forms.
While white is important it is more important to understand that many white products will not retain their original reflectance once they have been in place and exposed to the environment. A better measure is the aged reflectance values that the materials achieve and that they exceed a certain value in order for them to still be considered energy efficient.
It is also important to recognize that the environment and exposure can certainly deposit debris and residue on the roof and that some materials can develop growth on their surfaces. Systems that can remain clean or be cleaned without loss of integrity are more viable for long-term energy efficiency.